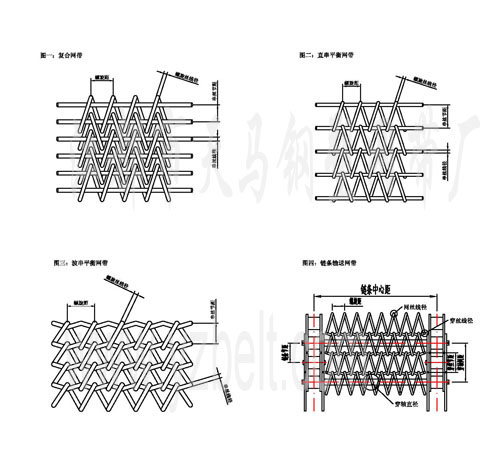
我国成全球金属能承受压力的容器主要生产基地之一 行业正呈高效节能化、一体化发展趋势
时间: 2024-12-04 02:30:59 | 作者: 企鹅电竞网址

根据观研报告网发布的《中国金属能承受压力的容器行业现状深度研究与投资前景分析报告(2024-2031年)》显示,金属能承受压力的容器是石油化学工业通用机械制造业的重要分支,也是装备制造业的重要组成部分。金属能承受压力的容器产品大范围的应用于石油、化工、机械、冶金、能源、航空航天等领域,在上述领域的生产、运输、反应等环节发挥着不可或缺的作用。
金属能承受压力的容器通常指用金属材料制造成的能承受压力的容器,是能够盛装气体或液体,具有一定功能、承受很多压力的密闭设备。按照工艺过程划分,金属能承受压力的容器大致可分为反应容器、换热容器、分离容器、储运容器四大类。
金属能承受压力的容器行业产业链较为完整。其产业链上游为原材料,不锈钢板、碳钢板、特材板、不锈钢管、碳钢管、特材管和锻件等。这类原材料采购价格波动与钢材市场行情报价的波动具有较强关联性。产业链下游为应用领域,括但不限于石油、化工、核电、太阳能、航空航天、海洋工程等行业。金属能承受压力的容器产品的需求与下业固定资产投资紧密关联。而上述行业景气度的提高将会带动相关固定资产投资的增加,进而带动金属能承受压力的容器需求的增长。
金属能承受压力的容器行业属于装备制造业,我国装备制造业是为国民经济与国防建设提供各类技术装备的制造业,具有产业关联度高、带动能力强和技术上的含金量高等特点。装备制造业发展水平是一个国家综合国力的重要体现,国家重大装备制造更是事关国家经济安全、国防安全的战略性产业。
近年来,随着“制造兴国”“碳达峰、碳中和”等一系列战略目标的提出,我国陆续出台了多项支持能源转型、推动制造业升级的产业政策。例如《中国制造 2025》提出:到 2025 年,具有我国自主知识产权的高端装备市场占有率能获得大幅的提升,核心技术对外依存度显而易见地下降,基础配套能力明显地增强,重要领域装备达到国际领先水平;同时也加强财政资金对制造业的支持,重点投向高端装备等制造业转变发展方式与经济转型的关键领域,为制造业发展创造良好的政策环境。
《国民经济和社会持续健康发展第十四个五年规划和2035年远大目标纲要》提出我国要大力提倡发展核电、天然气、太阳能、氢能等清洁能源和可再生资源等战略新兴行业相关项目。《人机一体化智能系统发展规划》中亦提出,要立足制造本质,紧扣智能特征,以工艺、装备为核心,以数据为基础,依托制造单元、车间、工厂、供应链等载体,构建虚实融合、知识驱动、动态优化、安全高效、绿色低碳的智能制造系统。
基于良好的发展环境和下业需求一直增长的带动下,我国能承受压力的容器市场规模逐年上升,其在国民经济中的重要性持续增强。多个方面数据显示,2023年我国能承受压力的容器市场规模达到2100亿元左右。预计到2027年这一市场规模有望超过3000亿元。
我国金属能承受压力的容器行业发展于20世纪五十年代,当时是中国石化集团南京化学工业有限公司化工机械厂的前身南京永利宁厂机械分厂试制成功中国第一台多层包扎式高压容器,开创了我国制造高压容器的历史,这一成就得到了国务院的嘉奖。随后《人民日报》专门发表了题为《自己动手制造更多的工业设施》的社论,引起了行业广泛关注。且到了六十年代,我国在金属能承受压力的容器领域已经具有一定的制造水平,国内中小型化肥厂、各种化工厂以及炼油厂所用的能承受压力的容器,已经基本实现国产化。
进入21世纪以来,随着我们国家宏观经济的快速地增长,石油、化工、机械、核电等行业的市场规模持续扩大,金属能承受压力的容器制造业在技术水平、产品质量、市场规模等众多方面实现了全面提升。预计随经济的持续不断的发展和转型,大型、特种能承受压力的容器的使用将日益增多,未来金属能承受压力的容器行业将会呈现大型、特种产品主导、信息化应用普及、行业标准国际化的发展态势。
经过多年的发展,我们国家金属能承受压力的容器制造业的发展经历了一个从无到有、从小到大、从混业到专业的发展历史。目前我国已发展成为全世界金属能承受压力的容器行业最重要的生产基地之一,保有量逐年增长,并且在技术水平、产品质量等众多方面已经实现全方面提升,高端、重型能承受压力的容器设备已基本不再依赖进口,部分技术难度高、制造工艺复杂的关键核心设备已经掌握自主知识产权,成功实现了国产化,甚至少数产品已接近国际领先水平并进入国际市场。多个方面数据显示,截至2022年我们国家金属能承受压力的容器保有量达到497.15万台,2014-2022年期间CAGR为5.55%。
值得注意的是,虽然近年我们国家金属能承受压力的容器得到了较大发展,在技术水平、产品质量等众多方面已经实现全方面提升,但现阶段仍处于工业化进程中,制造业大而不强,市场还存在自主创造新兴事物的能力偏弱、关键核心技术与高端装备对外依存度较高、缺乏世界知名品牌、资源能源利用效率低及产业体系不合理等问题。
近年来,得益于我国石油石化、钢铁冶金、机械等行业产量和消费量一直增长,带动了上游金属能承受压力的容器行业的快速发展。根据能源发展规划,未来我国在石油石化等领域将继续保持健康平稳的发展形态趋势,这也表明金属能承受压力的容器行业仍有较大的发展空间。同时“碳中和”“碳达峰”背景下,核电、天然气、太阳能等清洁能源以及环保、生物基材料、军工等战略新兴行业也给金属能承受压力的容器带来了新发展空间。
例如在石油化学工业方面:“十三五”期间,国内石油化学工业行业“基地化、园区化、一体化”发展的理念慢慢的变成了共识,集聚发展的空间格局大框架基本形成。2015 年发布的《石化产业规划布局方案》提出重点建设上海漕泾、浙江宁波、广东惠州、福建古雷、大连长兴岛、河北曹妃甸、江苏连云港七大世界级石化基地,推动我们国家石化行业高质量发展。
随着以七大基地为主基调的新建、改建炼化一体化项目的加速推进,我国炼油能力持续稳步提升。2022年我国的炼油能力增至每年9.2亿吨,超过美国变成全球上最大的炼油国,反映我国石化产业高水平发展实现了新跨越。到2023年国内炼油总能力达到9.36亿吨/年,炼厂开工率为79.1%。
与此同时,为避免炼油产能无序扩张,推动行业转变发展方式与经济转型,发改委等四部门联合发布《关于促进炼业绿色创新高水平发展的指导意见》,明白准确地提出到2025 年,国内原油一次加工能力控制在 10 亿吨以内,千万吨级炼油产能占比 55%左右,各地要依法依规推动不符合国家产业政策的 200 万吨及以下的炼油装置有序淘汰退出,新建炼厂的常减压装置规模不能低于 1,000 万吨/年。截至 2023 年底,我国仍有 32 家 200 万吨/年及以下常减压装置的炼厂,同时以炼油产能“红线 亿吨/年计算,我国未来大型炼厂新增及替换产能接近 1.3 亿吨/年。
核电方面:近年能承受压力的容器在核电行业应用广泛,主要有蒸汽发生器、反应堆能承受压力的容器、稳压器、反应堆冷却剂管道、余热排出系统热交换器等。
近年人们对核能的应用重视程度不断的提高,而核能最主要的应用就是核能发电,其装机容量和发电量呈增长趋势。2022年以来,我国新核准核电机组10台,新投入商运核电机组3台,新开工核电机组6台。截至目前,我国在建核电机组24台,总装机容量约2,681万千瓦,继续保持全球第一。商运核电机组54台,总装机容量5,682万千瓦,位列全球第三。截至2023年,我国核电总装机容量5,691万千瓦,占全国电力装机总量的1.9%,发电量为4,347.2亿千瓦时,同比增加4.1%,约占全国总发电量的4.5%,核能发电量达到世界第二。
光伏方面:随着环境形势日益严峻,国家对环境保护的重视程度不断的提高。受此影响,光伏产业在国家政策的引导和技术进步的推动下实现了加快速度进行发展。依据数据显示,2023年,我国光伏新增装机容量达到216.88GW,同比增长148%,累计装机容量达到609.5GW,同比增长55.2%;创下历史上最新的记录。预计随国家“碳达峰、碳中和”工作的推行,以及光伏发电成本的逐步降低,我国光伏行业仍将保持较快增长。
随着光伏行业的发展,也带动了光伏上游多晶硅的发展。2022 年全年光伏产业链各环节产量再创历史上最新的记录,全国多晶硅、硅片、电池、组件产量分别达到 82.7 万吨、357GW、318GW、288.7GW,同比增长均超过 55%。2023 年 1-10月,全国多晶硅、硅片、电池、组件产量分别为 108 万吨、440GW、393GW、360GW。
而多晶硅与颗粒硅的生产需要大量使用换热能承受压力的容器、分离能承受压力的容器等相关设备,并且对设备的质量以及可靠性要求很高,近年来光伏产业的持续快速地发展为高端能承受压力的容器带来了广阔的市场空间。鉴于我国光伏行业持续高景气,需求增量将通过硅片市场紧缺传导至上游能承受压力的容器设备制造商。
目前我们国家金属能承受压力的容器行业也呈现出高效节能化、清洁能源领域延伸化、模块化及一体化的发展的新趋势。一方面随着“碳中和”“碳达峰”相关规划政策的陆续出台,石油、化工、火力发电等传统行业开始向绿色、环保、节能方向转型发展;另一方面国家政策大力培育核电、天然气、太阳能等清洁能源以及环保、生物基材料、军工等战略新兴行业;此外随着下游客户对生产环节要求的细化,金属能承受压力的容器的许多业务都应该要依据客户需求定制,金属压力容器的生产将逐渐打通上下游产业链,趋向于业务一体化。